|
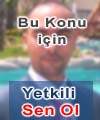 |
Celik Konusunu
Araştıran , Geliştiren Akademi Yetkilisi
Kimdir? |
 |
Oerlikon'dan Kaynak Teknolojisi |
|
Erdinç Özkara - (İnş. Müh.) |
DEPREME DAYANIKLI YAPILAR IÇIN KAYNAK UYGULAMALARI
Deprem esnasinda ölüm ve yaralanmalar, yapilarin yikilmasindan kaynaklandigina göre, yapilarin deprem esnasinda nasil davrandigi konusu incelenerek azaltilabilir. Bu tip bilgilerin kazanilmasi uzun süreli incelemeler gerektirmektedir. Çünkü deprem olus zamanlari düzensizdir ve çogunlukla da uzun araliklarla gerçeklesmektedir. Bu tip incelemeler için yapilara sismik kayit cihazlari yerlestirilebilir ve deprem aninda istenen bilgilere bu yolla ulasilabilir. Bu bilgiler isiginda, depreme dayanikli bina tasarimlarinin yapilmasi mümkün olabilir.
Ülkemiz topraklarindaki yerlesimin ortalama yüzde 95’ine yakin bir bölümü deprem bölgesinde oldugunu düsünürsek, bizlerin felaket olarak niteledigi aslinda sel, firtina gibi afet olan depremin etkilerini ve kayiplarini en aza indirmek için uzun dönemde bu tip çalismalarin baslatilmasi kisa dönemde de acil önlemler almak gerekliligi kendiliginden ortaya çikar. Kisa dönemde alinacak tedbirlerin basinda bundan sonra insa edilecek binalarin zemin etüdleri ile belgelenmis zeminler üzerine insaat mühendisleri tarafindan statik ve dinamik yükler hesaplandiktan sonra dogru bir tasarim ile projelendirilip uygun malzemeler kullanilarak egitimli personel tarafindan insa edilmesi ve tüm bu süreçlerde kontrol sisteminin eksiksiz olarak uygulanmasi gelmelidir. Bu anlamda en büyük görev uzmanligini ispat etmis ilgili sanayi ve denetim kuruluslarina, üniversiteler, merkezi ve yerel yönetimlere düsmektedir. Tüm bunlarin yani sira, depremlerde can ve mal kayiplarinin en aza indirilmesinin diger bir yolu da, dünyada meydana gelen depremleri büyüklükleri ve sonuçlari itibariyle incelenerek, kullanilacak sistem açisindan en uygun yapi modellerinin belirlenmesi ve ülkemizde uygulanmasidir. Bu noktada incelenmesi gereken konularin en basinda betonarme ve çelik yapilarin depreme karsi davranis özellikleri gelir.
Depreme dayaniklilik açisindan betonarme mi, yoksa çelik konstrüksiyonlarin mi daha güvenilir oldugu konusu Insaat Mühendisligi biliminin yetki alanina girmektedir. Bunlarin deprem sirasindaki davranislari konusunda fikir sahibi olabilmek için yakin tarihte gerçeklesen depremleri ve sonuçlarini incelemek faydali olacaktir.
1985 Mexiko City Depremi
19 Eylül 1985’de Richter ölçegine göre 8.1 büyüklügündeki depremde binlerce kisi hayatini kaybetmis, bir çok bina yikilmis ya da hasar görmüstür. Büyük felaketler karsisinda çok kritik öneme sahip olan yerel saglik merkezleri de bu depremde ciddi hasarlara ugramistir. Bunlarin arasinda 1970 yilinda insa edilen 11 katli Juares Hastanesi’de vardi. Bu binalarin enkazinda yapilan incelemelerde dört adet alin kaynakli çelik çubuk bulunmustur. Betonarme binalarin insaasinda üzerinde durulmasi gereken en önemli konu çelik çubuklarin birlestirilmesidir.
Ülkemizde bu tip çelik çubuklarin baglantilarinda kaynak kullanilmamaktadir. Bu çubuklarin birlestirilmesinde pek çok metod olmasina ragmen bazi ülkelerde çok katli binalarda sikça kullanilan yöntem kaynaktir. Betonu güçlendiren çelik (insaat çeligi) için kaynak prosedürleri pek çok ülkedeki insaat yönetmeliklerinde bulunmaktadir. Bu sartnameler genellikle kaynagin temel konularini içerirler. Örnegin çeligin kimyasal kompozisyonu, kaynak agzi tasarimi, kaynak agizlarinin hazirligi, uygun elektrod seçimi, kaynakçi sertifikalandirilmasi, gözetim ve kalite kontrol gibi. Mexico City depreminde hasarin en fazla oldugu bölgede yikilan alti binadan 60 insaat çeligi numunesi toplanmis ve kaynak teknolojisi açisindan durum degerlendirildiginde;
1. Insaatlarda kullanilan çeliklerin yüzde 90’ina yakin bölümünün kimyasal analizleri nedeniyle kaynak kabiliyetlerin son derece sinirli ve özel kaynak prosedürlerine ihtiyaç oldugu görülmüstür. Kaynak kabiliyeti üzerinde olumsuz etkileri olan fosfor ve kükürt elementlerinin insaat çelikleri içinde bulunma miktari yillara göre düsüs göstermis olsa da bu yikimlar önlenememistir.
2. Kaynak agizlarinin uygun hazirlanmadigi, dolayisiyla nüfuziyetin yetersiz oldugu ve kaynakta gözenekler olustugu
3. Uygun ilave metalin seçilemedigi
4. Uygulamada ise curuf kalintilarindan ve pasolar arasi sicakligin kontrol edilmemesinden dogan çatlaklarin olustugu tespit edilmistir. Sonuç olarak mekanik mukavemeti düsük insaat çeliklerinin kullanilmis oldugu ve kaynak uygulamalarinda kaynakçilarin yeteri kadar egitimli olmadigi anlasilmistir.
1994 Northridge Depremi
17 Ocak 1994’teki Northridge (Kalifoniya) depremi öncesinde insaat mühendisleri özel tasarima sahip çelik konstriksiyonlu binalarin siddetli yer hareketlerine direnç gösterecegi ve çok sinirli düzeyde hasar olusabilecegine inaniyorlardi. Fakat deprem sirasinda 100’den fazla çelik iskeletli yapida kirilmalar oldu. Kirilmalar iskeletin kiris-kolon birlestirme bölgelerindeki kaynaklarda basladi. Baslangiçta kirilmalarin kaynak isçiligi ile ilgili oldugu düsünüldüyse de insaat öncesi malzeme test degerleri ve depremin hemen ardindan yapilan testler birlestirme bölgelerindeki standartlara uygun kaliteli kaynak isçiliginin dahi kirilmalari önleyemedigini gösterdi. Zemin özellikleri ve yer sarsintilari dikkate alinarak insaat yönetmeliklerinin hazirlandigi bölgede de pek çok binada hasar oldu. Sonuç olarak bu insaat yönetmeliklerinin yeterliligi sorgulandi ve1994 ‘te acil bir yönetmelik degisikligine gidildi.
1995 Kobe Depremi
Japonya’da bulunan Kobe sehrinde 17 Ocak 1995 sabahi Richter ölçegine göre büyüklügü 7.2 siddetindeki depremde yaklasik 5.500 kisi hayatini kaybetti. 27 bin kisi yaralandi. 150 bin bina hasar gördü ve 30 binden fazla kisi acil yerlesim bölgelerine tasindi. Depremde ahsap binalarin disinda, betonarme ve çelik konstrüksiyon binalarda da hasarlar meydana gelmisti. Bu depremin en çarpici sonuçlarindan biri de çelik konstrüksiyonlardaki hasarin büyük kisminin alçak, 2-5 katli binalarda meydana gelmesi ve yedi katin üzerindeki binalarda yikilma olmamasiydi. Binalarin yüksekligine ve tasarimina göre kaynakli baglantilarin sekli degismekle birlikte depremde hasar gören bir çok alçak binada genellikle köse kaynaklari kullanilmis oldugu görüldü.
Çelik Yapilarda Olusan Hasarlarin Kaynakla Iliskisi Northridge ve Kobe depremleri sonrasinda yapilan arastirmalarda çelik konstrüksiyonlarda meydana gelen hasarlarin, kolon-kolon, kolon-kiris ve kolon-taban baglantilarinda olustugu görüldü. Bu baglantilarin büyük bir bölümü de kaynak ile yapilmisti. Kaynak hatalari nedeniyle olusan hasarlar asagidaki gibiydi:
1. Iç köse kaynaklarinda kaynak boylari kisa tutulmus, baglantilarda iyi bir nüfuziyet olusmamis ve hiçbir plastik deformasyon olmadan kirilma meydana gelmisti.
2. Eski tasarima sahip kolon-kiris baglantilarinda daha fazla hasar olmustu.
3. Kaynakla ilgili tüm prosedürlerin uygun oldugu hallerde bile çok yüksek plastik deformasyon nedeniyle olusan kirilmalar önlenememisti.
4. Ana konstrüksiyon disinda, binaya yapilan balkon, platform, çikinti v.b. eklerdeki kaynaklarin iyi kontrol edilmemesi sonucu binalarda ciddi yikimlar meydana gelmisti. Ayrica, diger depremlerde oldugu gibi Kobe depreminde de kaynakli baglantilarda gevrek kirilmalar oldugu gözlenmistir.
Gevrek kirilmanin olusmasini destekleyen, deprem aninda itici gücün olusmasi, tasiyici elemanlarda çatlak baslangicinin mevcut olmasi gibi tüm parametreler bir araya gelerek gevrek kirilmalari hizlandirmistir. Amerika’da yasanan Northridge depreminden sonra çelik konstrüksiyonlardaki hasar türleri belirlenmistir. Bu hasar tespitlerinden sonra hasarli binalarin tamirini yaparken ve bundan sonra insa edilecek çelik konstrüksiyonlu binalarin insaasinda dikkat edilmesi gereken tüm noktalari belirlemek için çesitli çalismalar yapilmistir.
Malzeme Seçimi ve Malzemenin Kaynak Kabiliyeti
Konstrüksiyon malzemeleri ve konstrüksiyon islemleri için hazirlanan endüstriyel sartnamelerde yapi performansi için çok kritik olabilecek mukavemet, tokluk ve diger özellikler genis bir spektrumda degisim göstermektedir. Mekanik özelliklerde karsilasilan bu degiskenlikler, baglanti mukavemetinin tahminini güçlestirmektedir.
Tasarimcilar, bina insaasi için kolay ulasilabilir ve her yerde bulunabilir malzemeleri seçmelidirler. Hangi malzemenin süneklik, kaynak kabiliyeti ve sismik kuvvetler açisindan uygun olacagini ve bu özelliklere sahip alternatif malzeme tiplerinin hangileri oldugunun da belirlenmesi gereklidir. Yatay kuvvetlere dirençli yapilarda kullanilabilecek pek çok yapi çeligi türü mevcuttur. Fakat, yapi çeliklerinin sismik direnç saglamasi için gereken özellikler halen tam olarak belirlenmis degildir. Bu tip çeliklerin deprem kuvvetlerine dirençli sistemlerde genel amaçli kullanilmasi için gereken kaynak kabiliyetine ve süneklige sahip olup olmadigi konusunda henüz bir ispat yapilmamis olmasina ragmen, istenen kaynak kabiliyeti ve süneklik özelliklerini saglayabilecegi tahmin edilmektedir. Bu tip çeliklerin kaynakli çelik konstrüksiyonlarda kullaniminin kabul edilebilirligini görebilmek için özel test prosedürleri ile test edilmelidir. Bu testler de gerçek kostrüksiyonda kullanilan malzeme ve kaynak yöntemi ile yapilmalidir. Kaynak kabiliyetini düsüren elementlerin, örnegin fosfor ve kükürtün çelik içinde bulunma miktari ilerleyen yillar içinde ciddi bir biçimde azalmistir. Karbon esdegerinin hesaplanmasi ise kaynak esnasindaki ön isitma ile pasolar arasi sicakliklari belirlemek için çok önemli bir araçtir. Her tip çeligin kimyasal analizi malzeme standartlarinda belirtilmistir. Çelik üreticileri her dökümde kimyasal analizleri yapmaktadir. Bazi ürünlerde mamül haldeki ürünün de analizi yapilabilir. Hadde test raporlarinin sertifikalari da müsteriye sunulabilir. Yapi çeliklerinin standartlarinda karbon, mangan, silis, fosfor ve kükürt miktarlari için üst limitler belirlenmistir. Ayni limitler, betonarme binalarda kullanilan insaat çelikleri için de belirlenmelidir. Bazi çeliklerde de diger elementler için alt ve üst limitler belirlenmistir. Çeligin mukavemetini, toklugunu, kaynak kabiliyetini ve korozyon direncini artirmak için krom, kolombiyum, bakir, molibden, nikel ve vanadyum eklenebilir. Sismik kuvvetlere maruz kalacak çeliklerin kimyasal analizi, ürün tipine ve ürünün sekline göre degisebilir. Kullanilan çelik mamüllerin süneklik ve tokluk özellikleri uygun test standartlarina göre yapilmali ve istenilen niteliklerde oldugu garanti edilmelidir. Kullanilan çeliklerde laminasyon olup olmadigi konusunda tahribatsiz test yöntemlerine basvurulmalidir. Fazla gerilimli kaynak birlestirmelerinin, lamellar yirtilmalara neden olacagi da tasarim sirasinda ve kaynak prosedürlerinin hazirlanmasi sirasinda göz önünde tutulmalidir.
Kaynak Yöntemleri
Çelik konstrüksiyonlarin kaynaklari pek çok kaynak yöntemi ile yapilabilir. Bunlar; örtülü elektrod, gazalti, özlü tel, tozalti ve elektro-curuf kaynak yöntemleridir. Kaynak yapilacak parçalarin formlarina, kalinliklarina, mevcut makine parkina ve uygun kaynak ilave metallerinin bulunabilirligine göre seçilen kaynak yöntemi, sartnamelerde belirlenen kaynagin geometrik formunu ve birlestirme mukavemetini saglamalidir. Çelik konstrüksiyonun birlestirme kaynaklari veya tamir kaynaklarinda kullanilacak kaynak yöntemleri önceden belirlenmis olmali ve bu sözlesmelerle sabitlestirilmelidir. Gerekiyorsa kaynak parametreleri konusundaki kisitlamalar da bu sözlesmede belirtilmelidir. Tamir kaynaklarinda ve bir çok birlestirme uygulamalarinda en çok kullanilan yöntem örtülü elektrod kaynak yöntemidir. Hangi kaynak yöntemi seçilirse seçilsin dogru kaynak sartlari altinda çalisilmadigi durumlarda zayif kaynaklar elde edilir. Bu nedenle kaynakçi egitimi, kaynak malzemesi ve kaynak makinasi seçimi, kaynak mahallinin saglik ve ergonomik uygunlugu son derece önemlidir.
Kaynak Prosedürü
Kaynak islemi, elektrod üreticilerin ve kaynak prosedürü sartnamesi (WPS, Welding Procedure Spesification) tarafindan belirlenen parametrelere uygun sekilde yapilmalidir. Örnegin, kaynak pozisyonu, elektrod çapi, kaynak akim türü, akim degeri veya tel sürme hizi, voltaj araligi, kaynak hizi ve elektrodun is parçasina olan mesafesi (ark boyu) WSP’de belirtilmis olmalidir. Bu yiksek kaliteli kaynaklar için gereklidir. Kaynak paremetreleri Proje Sartnameleri’nde Proje Çizimleri’nde Imalat Sartnameleri’nde açik bir sekilde belirtilmelidir. Kaynak paremetreleri her elektroda göre degisebilir. Ayni standarttaki elektrodlarin veya özlü tellerin kaynak parametreleri de üreticiden üreticiye farklilik gösterebilir. Bu nedenle, kullanilacak kaynak paremetreleri, üreticinin tavsiye ettigi sinirlar içinde olmalidir.
Alternatif olarak kaynak prosedürünü kabul edebilmek için ana malzeme üzerine WSP’te önerilen kaynak yöntemini belirlenen kaynak parametreleri ile kaynak yaparak test edilmelidir. Kaynak hizi, WSP’de verilen kaynak agzi tasarimindaki yükseklik ve genislik degerlerini saglayacak ve bu degerleri asmayacak sekilde olmalidir.
Kaynak Ilave Metalleri
Çelik konstrüksiyonda kullanilan çelik türüne ve özelliklerine göre ilave metal seçimi çelik seçimi kadar önemli bir konudur. Daha önceki yillarda daha düsük mukavemetli çeliklerin kaynaginda düsük hidrojenli E 7018 türü elektrodlar yogn bir sekilde kullanilmis olsa da yüksek dayanimli çeliklerde daha yüksek mukavemet degerlerine sahip elektrodlar kullanilmalidir. Kullanilacak her tür kaynak malzemesinin düsük hidrojenli olmasi gerekir. Tamamen kapali özlü tellerin ve tozalti tellerin nem almasi söz konusu olmadigindan, düsük hidrojenli elektrod (tel) olarak kabul edilebilir. Kenetli özlü teller bir miktar nem alabilecegi için hidrojen açisindan riskli olabilir.
Tam nüfuziyetli kiris-kolon baglantilari veya üç eksenli yüklemelerin mevcut oldugu baglantilar v.b. kritik birlestirme noktalari için, ilave metalden beklenen tokluk degerleri belirlenmi olmalidir. Kaynak ilave metali de bu tokluk degerini saglamalidir. Elektrodun uygunlugu konusunda yapilan tüm testler ve sertifikalar iyi dökümante edilmelidir. Her elektrod sinifi, bu gruptaki her üretici ve her marka için bu testler ayri ayri yapilmalidir. Kullanilacak elektrodun özellikleri ve kaynak sartlari ile ilgili bilgiler ögreticiler tarafindan saglanmalidir.
Northridge ve Kobe depremleri sonrasinda çelik konstrüksiyonlardaki kirik yüzeylerede yapilan incelemelerde, kirilmalarin uygun olmayan elektrod kullanim ve kaynak prosedürleri ile ilgili oldugu gerçegi ortaya çikmistir. Bariz hatalar ise, yüksek imalat hizi, standartlarda belirlenen kaynak dikis formundan daha genis ve daha yüksek kaynak dikislerinin yapilmis olmasidir. Bu tip genis kaynak dikisleri ile saglanan kaynak isi girdisi, isidan etkilenen bölgelerde tane büyümesi ve bunun sonucunda malzemenin tokluk degerinin düsmesine neden olmaktadir. Northridge depreminden etkilenen binalardaki kaynaklari incelerken en önemli problemlerin kök açikligi, kaynak bölgesine ulasilabilirlik, elektord çapi seçimi, elektrodun ana metale uzakligi, kaynak pasosu yüksekligi, kaynak pasosu genisligi, kaynak hizi, tel sürme hizi, akim ve voltaj degerleri gibi kaynak paremetrelerinde yapilan hatalar oldugu görülmüstür. Bir kaynak birlestirmesinde birden fazla kaynak yöntemi veya birden fazla ilave metal türü kullanildiginda kullanilan bu kombinasyonlarin birbiri ile uyumu konusunda emin olunmalidir. Tüm bu kararlarda ciddi testler yapilmasi ve bu test sonuçlarinin yazili olarak belgelenmesi ve saklanmasi da sarttir.
Kullanilacak elektrodun çapi, kaynak pozisyonuna ve malzeme kalinligina göre seçilmektedir. Bir elektrod çapinin saglayabilecegi optimum bir kaynak dikisi genisligi vardir. Bu optimum kaynak dikisi genisligi optimum mekanik özellikleri saglamalidir. Kabul edilebilir limitlerin disindaki kaynak dikis boyutlari kabul edilemez kaynak kalitesi sonucunu verebilir.Seçilen elektrod çapi ile elde edilen kaynaklarin mekanik degerleri, sartnamelerde istenen mekanik degerleri saglamalidir. Onayli WSP’lerde tüm diger kaynak parametreleri gibi kullanilacak elektrodlarin çaplari da belirtilmis olmali ve parametrelerde kaynak islemi gerçeklestirilmelidir.
Kobe depreminde meydana gelen yüksek hizli yer hareketinin (104 cm/sn) neden oldugu sismik kuvvetler alisilmisin disindaydi. Bu da yapilarda dinamik dayanim sinirlarini zorlamistir. Neticede kaynak metalin çentik darbe dayaniminin olabildigince yüksek olmasi binayi böyle zor anlarda nefes aldirabilecektir. Dolayisiyla, elektrodlarin mekanik degerleri standartlarin belirledigi alt sinirlarin üzerinde olsa da mekanik özellikleri en yüksek olan elektrodlar tercih edilmelidir.
Ön Isitma ve Pasolar Arasi Sicakliklar
Kaynak standartlarinda da belirtildigi gibi ana metal türüne ve kalinligina göre ön isitma sicakliklari ve sartlarina uyulmalidir. Kaynakta veya isidan etkilenen bölgede olusabilecek çatlaklar önlenmelidir. Bu tip çatlaklarin bir türü hidrojen çatlagidir. Önem sirasina göre hidrojen çatlagi olusturma egilimini azaltan faktörler sunlardir: 1. Daha düsük hidrojen miktari içeren kaynak malzemeleri kullanmak, 2. Daha yüksek ön isitma ve pasolar arasi sicakliklar uygulamak, 3. Kaynak sonrasi tav yapmak, 4. Sogumayi yavaslatmak.
Sismik yüklemelere maruz yapilarin tamirinde ve imalatinda yalnizca düsük hidrojenli elektrodlar kullanilmalidir. Uygun ön isitma ve pasolar arasi sicakliklar korunmalidir. Ön isitmanin ve pasolar arasi sicakliklarin kontrolünün kaynak açisindan belli amaçlari ve yararlari vardir. Yeni konstrüksiyonlar için standartlarda belirlenen sartlar genelde yaterlidir. Yüksek yüklerle yüklenen ön-gerilimli tamir kaynaklari daha yüksek ön isitma seviyesine ihtiyaç duyabilirler.
Hidrojen çatlaginin olusumu için hidrojen kontrolü, uygun ön isitma ve pasolar arasi sicakliklarin etkisi son tav ve yavas sogutma metodlarindan daha güçlüdür. Eger tüm parça ön isitma yapilmadiysa ki, yapisal uygulamalarda ön isitma yapmak çok zordur, yavas sogumanin yarari ön isitma ile karsilastirildiginda çok sinirlidir. Mühendisler uygun ön isitma ve düsük hidrojenli elektrodlarin kullanimi konusunda cesaretlendirilmelidir. Eger yapilan uygulamalar çatlagi önlemekte yetersiz kalirsa, çatlamanin nedenlerini ortaya çikartabilecek ve uygun önerilerde bulunacak kaynak mühendislerine danisilmalidir.
Düsük hidrojenli elektrodlar kullanildigi ve uygun ön isitmanin yapildigi bazi birlestirme kaynaklarinda son tav ve yavas sogutma gerekmeyebilir. Fakat genel kaynak uygulamalarina göre ön tav yapilmasi öngörülen kaynaklarda, son tav ve yavas sogutma uygulamalari da yapilmalidir. Atölyede yapilan birlestirmelerde ön tav, son tav ve pasolar arasi sicakliklari uygulamak daha kolay olsa da insaat bölgesinde bu uygulamalara sadik kalmak oldukça zordur. Fakat konunun önemi dikkate alindiginda gerekliligi de açiktir.
Tamir kaynaklari genellikle yüksek gerilimler altinda yapilmaktadir. Bu kaynaklar yapilirken mevcut yükler, baska desteklerle veya askilama gibi uygun yöntemler kullanilarak dengelenmelidir. Tamir uygulamalarinda daha yüksek ön isitma yapmak, kirilgan faz olan martensitin olusumunun önlenmesi ve daha sünek – tok yapiya sahip olan beynit veya ferrit-perlit olusumu için önemlidir.
Ön isitma sicakligi, kaynak bölgesi ile ayni kalinliktaki bir yerden ve kaynaktan en az 7-8 cm uzakliktan ölçülmelidir. Farkli kalinliktaki malzemeler kaynak ile birlestirilecegi zaman kalin olan malzemeye göre ön tav ve pasolar arasi sicaklik sartlarina uyulmalidir. Kritik uygulamalarda ve onayli WSP’lerde pasolar arasi sicakliklar hiçbir zaman 300 C dereceyi geçmemelidir. Daha yüksek sicakliklar, ancak bu yüksek sicakliklarla test yapilip onaylandiginda kullanilabilir.
Son Tav
Kaynak islemi bittikten sonra, kaynak bölgesine en fazla 300 C dereceye kadar sicakliklarin uygulanmasina son tav denir. Son tav sicakligi ve süresi malzeme tipine, kesit kalinliga v.b. faktörlere göre belirlenmelidir. Son tav uygulamasi bazi çatlama egilimlerinin önlenmesi bakimindan faydali olabilir.
Son tavin amaci, kaynak bölgesinden ve isidan etkilenen bölgeden hidrojenin diffüzyon yoluyla çikisini hizlandirmak ve hidrojen kirilganligi nedeniyle çatlamayi engellemektir. Hidrojenin 450 C derecedeki kaynak metalinde diffüzyon hizi saatte 2.5 cm’dir, fakat 70 C derecedeki kaynak metalinde diffüzyon hizi ise ayda 2.5 cm’dir. Birlestirme kaynaklarinda son tav yapilmasi gerekiyorsa tüm sartnamelerde son tav kosullari belirtilmeli ve bu kosullara uyulmalidir.
Kontrollü Sogutma
Çogu kaynakta soguma radyasyon ile degil de isi iletimi yolu ile olur. Kalin kesitli malzemelerin kaynaginda, ortam sicakligi, hizli sogumaya neden olacaksa ve/veya yüksek yükler nedeniyle artik gerilimler olusabilecek ise yavas sogumanin nasil yapilacagi sartnamelerde belirtilmis olmalidir.
Kaynagin soguma süresi, istenen yalitim seviyesi, kaynak bölgesinin (parçanin) sicakligina ana metalin kalinligina ve ortam sicakligina baglidir. Daha kontrollü sogutma yani, soguma hizinin belli bir seviyede olmasi genellikle gerekmez, fakat yüksek yükler altindaki kaynaklarda ek bir avantaj saglayabilir.
Metalurjik Gerilimi Arttiran Faktörler
Ön isitma yapmadan ark ile oyma, alevle kesme, puntalama v.b. metalurjik süreksizlikleri takip eden kaynak isleminin yapilmasina kesinlikle müsaade edilmemelidir. Ark ile oyma veya alev ile kesme herhangi bir ön tav gerektirmez fakat, bu islemin ardindan yapilan kaynak islemi, isidan etkilenen bölgenin yüksek sicakliklarda tavlanmasina neden olur ki, bu da malzemenin mekanik özelliklerinde bozulmaya neden olur. Gayri ihtiyari olarak yapilan bu hasarlar, mühendisler tarafindan onayli bir yöntemle, kaynak standartlarina ve WSP’lere uygun sekilde tamir edilmelidir. Tozalti kaynak yöntemi ile kaynak yapilmasi durumu hariç, diger durumlarda kaynak öncesinde yapilmasi gereken ayni ön tavin, puntalama kaynaklari öncesinde de yapilmasi gereklidir.
Ark baslangiçlari, metalurjik gerilimlere neden olabilecegi için rastgele yapilmamalidir. Kaynak metali disinda yapilacak ark baslangiçlarinin, ana metal üzerinde olmasindan kaçinilmalidir. Ark baslangicinin yapildigi yüzeyin kusursuzlugundan emin olmak için ark baslangicindan kaynaklanan çatlaklar ve hatalar düzgün bir sekilde taslanmali, gözle kontrol edilmeli ve bu tip hatalarin tamiri uygun sekilde yapilmalidir.
Kaynak Hazirligi
Kaynak hazirliginda ve kaynakta kullanilacak kaynak ekipmanlari ve termik kesme ekipmanlari kaliteli kaynaklar verecek sekilde tasarlanmis ve üretilmis olmalidir. Kaynak ve kesme sirasinda hataya neden olabilecek ve kaynak uygulayicilarinin istenen kaynak prosedürüne göre çalismasini engelleyecek kaynak ve kesme ekipmanlari kullanilmamalidir. Kaynak makinasinin istenen akim ve voltaj degerlerini kaynak süresince sagliyor olmasi gerekir. Akim ve voltaj kontrolünün çok düsük düzeyde oldugu ve özellikle kademeli salterle ayar yapilan kaynak transformatörleri ile kaynak nüfuzeti her zaman kontrol edilemeyecegi için bunlarin kullanimindan kaçinilmalidir. Elektrik arki ile kesme, oyma ve oksi-gaz kesme islemleri, malzemelerin hazirliginda kesme veya düzeltme amaçli kullanilmaktadir.
Plazma kesme en fazla kullanilan elektrik ark kesme yöntemlerinden biridir. Diger termik kesme yöntemlerinin kullanimi mühendislerin kontrolünde testler yapilarak olumlu sonuç alindigi durumlarda kullanilabilir. Oksi-gaz ile kesme, su verilmis ve temperlenmis veya normalize edilmis çeliklerle kullanilamaz.
Hava sicakligi –18 C dereceden düsük oldugunda ve kaynak yüzeyleri islakken kaynak yapilmamalidir. Ayrica kaynak yapilacak metal yüzeyler, yagmura, kara veya yüksek rüzgar hizina maruzken veya çalisan kisiler bu tip hava sartlarina maruzken kesinlikle kaynak yapilmamalidir.
Kaynak agizlari düz veya düzgün olmali, yüzeyde kaynak mukavemetini ve kalitesini kötü yönde etkileyecek çatlak, yirtik, gözenek veya diger süresizlikler olmamalidir. Kaynak ile birlestirilecek yüzeylerde ve kaynaga yakin bölgelerde pas, kir; curuf, nem, yag ve diger yabanci maddeler bulunmamalidir. Bu maddeler kaynak kalitesini kötü yönde etkiler veya zararli dumanlar olusturabilirler. Zimparalarla düzeltilemeyen hadde izleri, pas içeren ince kaplamalar veya siçramaya karsi kullanilan kaynak spreyleri bazi sartlarda yüzeyde kalabilir. Kaynak yapilacak yapi elemanlarinin ne kadar önemli bir yapi elemani oldugu düsünülerek bu tip yüzey hatalarina izin verilip verilemeyecegine de karar verilebilir.
Termik kesme yapilirken dikkat edilmesi gereken en önemli konular kesimin, önerilen çizgilerden yapilmis olmasi ve yüzey düzgünlügünün standartlarda belirtilen ölçülerde olmasidir. Yüzey düzgünsüzlügü istenen limitlerden fazla ise taslama ile veya isleyerek yüzey düzeltilmelidir. Kesilen yüzeylerde curuf kalintisi olmamalidir. Kesme yaparken ortaya çikan hatalar kaynak ile tamir edilecek ise tamir kaynaklari da uygun bir prosedüre göre yapilmalidir.
Kaynak boyutlari ve uzunluklari tasarimda belirtilen isteklere ve çizimlere uygun olmalidir. Kaynakta veya kaynak yerinde yapilacak degisiklik, mühendisler tarafindan onaylanmis olmalidir. Yapilacak kaynakta çarpilma ve çekmeleri en aza indirmek için önlemler alinmalidir. Kaynak yapilacak parçalarin baglantisi yapilirken kök açikligi ve hizalamasi kaynak prosedürü sartnamelerine uygun olmalidir. Istenen ölçülerde kök asikligi saglanamazsa mühendislerin kontrolü altinda farkli yöntemler kullanilabilir, bu yöntemlerden bir tanesi de kaynak altligi kullanimidir. Yaygin olarak kullanilan altliklar seramik, bakir ve çelik altliklardir. Hangi tip çeliklerin kaynak altligi amaciyla kullanilabilecegi kullanilan ana malzemeye baglidir ve standartlarda kaynak altligi olarak kullanilabilecek çelikler belirtilmistir.
Puntalamada, ayni kaynak gibi yüksek kalite gerektirir. Oyulma, doldurulmamis kraterler ve gözenek gibi süreksizlikler tozalti kaynagindan önce giderilmelidir. Uygun olmayan kaynaklarin ve kaynak hatalarinin tamiri, mühendislerin hazirlamis oldugu prosedüre göre yapilmalidir.
Kaynakçilarin kaynak bölgelerine rahat ulasimi saglanmali, kaynak islemini hiçbir olumsuzluktan etkilenmeden gerçeklestirebilmelidir. Kaynakçilar uygun is güvenligi kiyafetleri giymeli, kaynak bölgesini daha rahat görmeyi saglayan ve kaynak isinlarinin zararli etkilerini önleyen özel kaynak camina sahip kaynak maskeleri kullanmalidirlar. Bas maskelerinin kullanilmasi kaynak yaparken kaynakçinin iki elini de serbestçe kullanabilmesi açisindan avantajlidir. Ayrica kaynak isinlari ile otomatik kararan ‘solarmatik’ maskeler, kaynakçinin arki yanlis noktadan baslatmasi ve ilerde çentik etkisi yaratacak kötü baslangiç noktalari olusturma risklerini de ortadan kaldirir.
Kaynakta Kalite Kontrol
Kalite güvence, bina sahibinin imtiyazindayken ve insaat yönetmelikleri tarafindan yönlendirilmekteyken, prensipte kalite kontrol müteahhitin sorumlulugundadir. Tüm isçiler ve kontrolörler istenen isi gerçeklestirmek için yeterli kalisifikasyona sahip olmali ve mühendisler tarafindan onaylanmis olan prosedürleri gerçeklestirebilmelidirler. Kaynaklarda kalite kontrolün saglanabilmesi için kaynakçilar ve kaynak operatörleri kalite planlari çalismalarinda ve kalite toplantilarinda alinan kararlar konusunda bilgi sahibi olmali ve belli bir seviyeye kadar kalite kontrolün içinde yer almalidirlar. Baglantilarin yapilmasi öncesinde baglantilar yapilarken kaynak hazirliklarinda puntalama sirasinda kaynak yapilirken ve kaynaktan sonra gerekli tüm testler ve kontroller yapilarak taahhüt dökümanlarinda belirtilen isçilik ve malzeme ihtiyaçlarinin saglandigindan emin olunmalidir. Kaynak hazirligini yapan kisiler ve kaynakçilar WSP dökümanlarina ve her baglanti ile birlestirmenin teknik çizimlerine sahip olmalidirlar. Yapilan her kaynakta hangi kaynakçi tarafindan yapildigi konusunda belirleyici bir markalama yapilmalidir. Kontrolörler, kontrol edilen ve kabul edilen her kaynak dikisinin kimin tarafindan kontrol edildigini ve kabul edildigini belirleyecek uygun markalamayi yapmalidirlar. Tahribatsiz muayenelerde de her kaynak dikisini ayiracak bir markalama sistemi kullanilmalidir. Tüm kontroller ve testler sertifikali kontrolörler tarafindan yapildigi gibi, kaynakçilarin kalisifikasyonu mutlaka uygun sertifikasyon sistemi ile yapilmis olmalidir. Tüm bu sertfikasyonlar, standartlarda belirlenen sekilde gerçeklestirilmelidir.
Kaynaklarin ve tüm islemlerin kalite kontrolü konusu, çok genis bir sekilde standartlarda belirlenmistir. Kalite güvence ihtiyaçlarinin ana hatlari asagidaki gibidir:
1. Kaynak kontrolörlerinin lideri mutlaka sertifikali olmalidir ve hatta mümkün ise yapisal çeliklerin kaynagi konusunda sertifikaya sahip olmalidir. Kaynagi göz ile kontrol eden ve diger kontrol islerini liderin süpervizörlügü altinda gerçeklestiren diger kaynak kontrolörleri de uygun sertifikaya sahip olmalidir.
2. Tüm kaynaklar standartlarda istenen sekilde kontrol edilmelidir.
3. Kaynak islemi bittikten sonra ve kaynak soguduktan sonra tam nüfuziyetli tüm kaynak dikisleri, tahribatsiz muayene metodlarindan o is için en uygun olani ile standartlarda istendigi gibi kontrol edilmelidir. Her kaynak için su islemler yapilmalidir:
A. Her onayli çizim ve spesifikasyon için malzeme tanimlamasi yapilmalidir.
B. Kolonlarda ve kirislerde lamimasyon olup olmadigi veya en azindan kaynak bölgesinin 15.cm. yariçapli dairesel çevresi standartlarda istendigi sekilde kontrol edilmelidir. Kontrol kaynaktan hemen sonra yapildiginda is kaybi daha az olmaktadir.
C. Onayli bir Kaynak Prosedürü Spesifikasyonu (WSP) hazirlanmis oldugundan emin olunmali ve bu WSP’ler her kaynakçi kaynagi yaparken kontrol edilmelidir. Her kaynak birlestirmesi için uygun WSP’lerden birer kopya bulunmalidir. WSP’lerin tatbik edilemedigi her kaynak kabul edilemez kaynak olarak düsünülmelidir.
D. WSP’lerde ve santiye çizimlerinde kullanilacak kaynak ilave metalleri belirtilmis olmalidir.
E. Kaynakçilarin sertifikasyonundan ve gerekli yeterlilik testlerinden geçirilmis olduklarindan emin olunmalidir.
F. Uygun akim ve gerilim degerlerinde çalisildigindan emin olmak için kalibre edilmis olan ampermetre ve voltmetreleri ile kaynak sirasinda pense ile is parçasi arasinda akim ve gerilim ölçülmelidir. Uzun veya uygunsuz kablo kesitleri ile çalisildiginda kaynak esnasinda istenen parametreler olusmayabilir.
G. Gerekli her kaynakta, standartlara göre göz ile muayene yapilmalidir. Üretim (kaynak) sirasinda asagidaki maddelerin çizimlerinde ve onayli WSP’lerde istendigi gibi oldugundan emin olunmali ve asagidaki faaliyetler dökümante edilmelidir.
1. Kaynak hazirligi 2. Ön isitma, pasolar arasi sicakliklar 3. Kaynak makinasi ayarlari: gerilim, kaynak esasinda iki kutup arasindan akim kablolarindan ölçülmelidir. WSP’lerde istenen parametrelerin disinda degerlerle yapilan kaynaklar kabul edilemez olarak görülmelidir. 4. Kaynak islemi 5. Kaynak paso sirasi ve kaynak dikisi boyutlari 6. Onayli WSP’lerde isteniyorsa kaynagin çekiçlenmesi 7. Kaynak altliklarinin ve kaynak baslangiç plakalarinin (pabuçlarinin) çikartilmasi, kaynak dikisinin taslanmasi, temizlenmesi ve WSP’lerde istendigi gibi köse kaynaklarinin güçlendirilme islemi 8. Bitmis kaynaklarin, WSP’lerde istendigi gibi son tav ve/veya yalitimlarinin yapilmasi
H. Standartlara göre ultrasonik metodlarla kaynak bölgesinin kontroli yapilmalidir. Mümkün olan yerlerde kaynaklarin iki yüzeyinde de kontroller yapilmalidir. Ayni zamanda kiris sonundaki flanslarin hem A hem de B yüzeyleri kontrol edilmelidir. Kontrolörlerin, istenen noktalara güvenli sekilde ulasabilmesi için müteahhit tarafindan gerekli sartlar saglanmalidir. Bu insaasi bitmis binalarda çok problem teskil etmese de insaa halindeki binalarda önemli bir problemdir.
Sonuç:
Deprem sirasinda çelik konstrüksiyonlarda olusabilecek hasarlari en aza indirgemek için uluslar arasi çalismalar halen devam etmektedir. Çelik konstrüksiyonlarin depremlere karsi mukavemetini etkileyen pek çok faktör vardir. Bunlar: zemin özellikleri ile baslayarak tasarim, malzeme seçimi, kaynak uygulamalari gibi pek çok ana faktör altinda sayisiz alt parametreye dayanmaktadir. Önemli olan tüm bu parametrelerin iyi irdelenerek bu parametrelerin hasarsizlik amacina göre seçimi, uygulanmasi ve uygulamalardaki kontrol asamalaridir. Çelik konstrüksiyonlarda kaynakli birlestirmelerin mukavemeti en önemli konulardan biridir. Tasarimlarda istenen birlestirme mukavemetinin elde edilebilmesi için kaynak islemi ile her tür parametrenin seçimi, seçilen parametreler ile kaynak uygulamasi ve kaynaklarin kalite kontrolü özenle yapilmalidir. Çelik konstrüksiyonun sahibinden baslayan sorumluluk zinciri, insaati taahhüt eden kisi veya kurumlarla devam ederken, bu sorumluluk zincirinin belki de en önemli halkalarini bizzat çalisanlar tamamlamaktadir. Depremde olusan sismik yüklemelere maruz kalan çelik konstüksiyonlar konusunda yapilan araitirma sonuçlarindan ortaya çikan tavsiyeler hiçbir zaman garanti saglayamayacagi gibi herhangi bir baglayiciligi olmamaktadir. Bu tip çalismalarin amaci öelik konstrüksiyon insaasinda çalisan tasarimcilara, mühendislere ve diger çelisanlara yapilan islerin prosedürleri degerlendirmesi, tamiri ve modifikasyonu için bir rehberlik yaparak depremden kaynaklanabilecek hasarlari en aza indirgemek oldugu göz önünde tutulmalidir. Uygulayicilar, bu önerileri gerçekte yaptiklari denemelerle ve bu denemelerin sonuçlarini profesyonelce inceleyerek daha iyi noktalara götürebilecekleri de açiktir. Bir zincirin mukavemetinin en zayif halkalari kadar oldugunu biliriz. Bu mantikla yapilara baktigimizda kaynagin önemini daha iyi anlariz.
Oerlikon Kaynak Elektrodlari ve Sanayii A.S.
Kaynak: http://www.tucsa.org
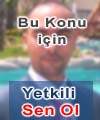 |
Celik Konusunu
Araştıran , Geliştiren Akademi Yetkilisi
Kimdir? |
 |
Oerlikon'dan Kaynak Teknolojisi |
|
Erdinç Özkara - (İnş. Müh.) |
Santiye | Celik | Yazim: 22.5.2005 | Hit : 554 BU SAYFAYI YAZDIR
Anasayfa >> Araştırıyoruz >> Çelik >> Oerlikon'dan Kaynak Teknolojisi
|
|
|
|
|
|
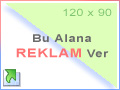 |
|
Bu sayfada Sadece Celik alanında faaliyet gosteren firma reklamları gösterilir. |
|
|
|